
- CNC DRIVER CONTROLLER SERIAL
- CNC DRIVER CONTROLLER DRIVERS
- CNC DRIVER CONTROLLER DRIVER
- CNC DRIVER CONTROLLER SOFTWARE
- CNC DRIVER CONTROLLER PC
STL’s are made with OpenScad and then converted either online or with Estlcam to.
CNC DRIVER CONTROLLER DRIVER
To get the best possible CNC driver / firmware setup, in combination with the CAD and CAM programs that are required, I tested the following setups with the Indymill hardware: 1) Reprap 3.3 & the Duet2wifi.
CNC DRIVER CONTROLLER PC
With a simple installation to a stand alone FlashCut or competitor driver box, it easily turns a Windows™-based PC into a CNC controller. Indymill CNC Controller -the final choice- and WHY.
CNC DRIVER CONTROLLER SOFTWARE
The USB-Powered Software and Signal Generator, capable of 100,000 digital pulses per second, forms the cornerstone of the FlashCut CNC product line. Our CNC systems provide machine tool automation from any Windows™ PC. Nema23 CNC 4 Axis Stepper Motor Kit 270oz-in 76mm 3A+TB6600 Driver 4.5A 10-45V+Mach3 USB Board Motion Control Card CNC Controller Kit w/ 350W 24V Power Supply for CNC Router Milling Engraver Machine. Plz.FlashCut CNC is the industry leader in powerful, easy-to-use, affordable CNC controls. With a simple installation to a stand alone FlashCut or competitor driver box, it easily turns a Windows-based PC into a CNC controller. Operating system is Manjaro (latest version, as it's a rolling release) I really hope there's a linux-"guru" somewhere that can guide me through this process, as I'm a totally newbee to linux, but I would really HATE to be forced back to Windows again. Our CNC systems provide machine tool automation from any Windows PC. Is there anyone "out there" that can help me here? What kind of board should I choose? Or maybe even better: Is there a stand-alone program, like LinuxCNC that supports my machine, using USB interface and NOT Com-ports (there's no com ports on my motherboard.)? -I do NOT want to change my operating system to LinuxCNC, if I can avoid that in any way. Hitting the "Board Info" option leaves me with BN: unknown VID: 1A SN: Upload any sketch to obtain it. I've followed the instructions here on this thread, but when I try to find the controller-board in the Arduino IDE - program, I just can't find anything usable. I've been searching high snd low, in order to find a usefull CNC-program to act between my mill and my linux-computer, but all I could find either didn't work or required a com port as interface.
CNC DRIVER CONTROLLER DRIVERS
3.4", and it came with drivers and software to windows only. It's the cheapest availble from E-bay, and the mainboard is named "Woodpecker CNC Camxtool v. I've just bought and build my CNC milling machine. Hopefully This instructables was helpful and your cnc machine is up and running! If something is wrong/missing feel free to point it out in the comments. When you have edited the config file you need to reupload the sketch to your board. The file has instructions and should be pretty straight forward to edit. You find the config file in the arduino library folder for grbl. Use of a screw terminal adapter makes connection to the type of drive in the image much easier. Optional support hardware can be employed to customize installation to suit user requirement. The single dongle plugs into the USB AUX port on the controller and needs to work with both devices. NOTE: The USB dongle usually comes with the wireless devices. Some settings (like corexy setup,variable spindle) needs to be changed trough the config.h. The USB CNC controller is compatible with the vast majority of motor drivers that use step/direction signals. Sherline/MASSO CNC Controller w/Driver Box.
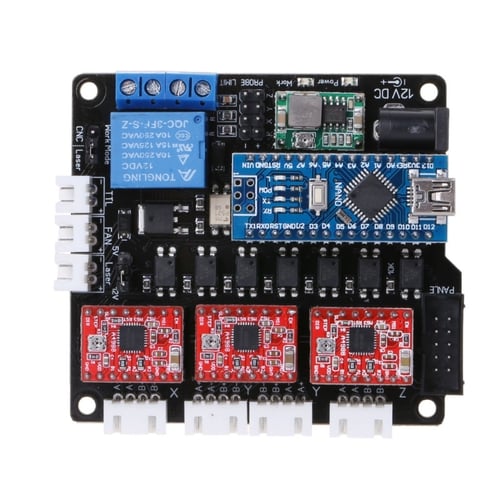
Make sure that your setting has been saved by typing $$ and checking the values. For example: typing $112=600 changes the z max rate to 600. To change a setting, type the identifier of the parameter (for example $100 for x steps) "=" and then the new value. Steps/mm needs to be calculated and the easiest way of doing it is by using prusas reprap calulator.
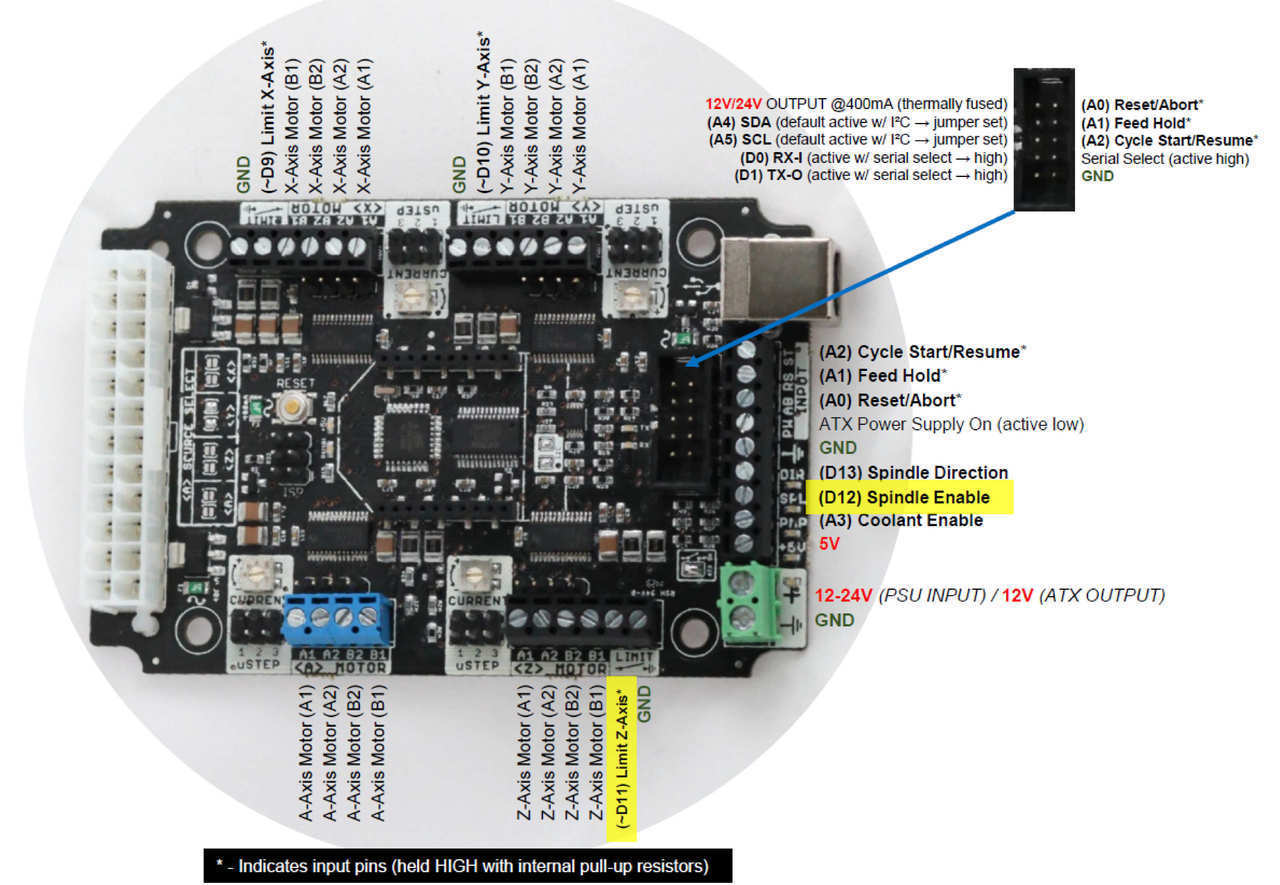

The most important part to change is the steps/mm. Type "$$" and a list of commands should appear, like this: You should see a message like this "Grbl x.xj " if you dont see the message, make sure that your are connected to the correct port and use the baudrate of 115200.
CNC DRIVER CONTROLLER SERIAL
To communicate with your board you need to open the arduino ide serial monitor. Now with firmware on your board you need to adapt grbl to your specific machine.
